Al via il nuovo ciclo di interviste firmate Panizzolo: Andrea Pensotti Com.Steel
Al via il nuovo ciclo di interviste firmate Panizzolo.Il primo intervistato è Andrea Pensotti, socio titolare di Com.Steel Spa.
Leader nel settore dei rottami metallici e ferrosi e con rapporti commerciali in tutto il mondo, Com.Steel Spa si propone come partner di aziende che operano con serietà, professionalità e nel rispetto dell’ambiente. Attualmente l’azienda tratta e commercia tutte le principali categorie di rifiuti metallici e ferrosi.

Come è nata Com.Steel e come state lavorando oggi? Ci può parlare di lei e dall’azienda?
Com.Steel nasce trent’anni fa da mio papà, mio fratello Edoardo e da me.
Edoardo gestisce tutta la fase commerciale e produttiva mentre io seguo la parte ambientale e amministrativa. Per i primi 10-15 anni ci siamo focalizzati sul trattamento dei cavi elettrici, con un impianto da 50-60 ton/giorno di prodotto macinato. Nel corso degli anni abbiamo poi deciso di diversificare il materiale trattato, andando quindi a toccare tutti i vari settori. Per i primi 14 anni la sede era situata in provincia di Lecco, in un sito di circa 5 mila mq. Nel momento in cui abbiamo iniziato a diversificare e sviluppare i vari settori di trattamento, è nata la necessità di maggiore spazio per gestire i flussi e la logistica. Ci siamo quindi trasferiti nel 2003 nell’attuale sede di Calusco d’Adda, in uno spazio di 20 mila mq. In questo modo siamo riusciti a sviluppare ulteriormente le varie tipologie di rottami metallici, specializzandoci nel mondo dell’acciaio inossidabile. In questi anni abbiamo iniziato a lavorare con le più grosse acciaierie italiane ed europee.
L’obbiettivo di oggi e del futuro di Com.Steel è quello di trattare più categorie possibili di rottami metallici e di massimizzare la valorizzazione dei metalli contenuti. Ciò ti permette di non essere succube dei capricci del mercato e di suddividere il rischio aziendale. Queste peculiarità ci hanno consentito di imporci come principale player nel mercato italiano e mondiale nell’acquisto e vendita di rottami metallici, tanto che da tre anni stiamo lavorando alla costruzione della nuova sede.
Potrebbe parlarmi del vostro organico aziendale? In quanti siete e come sono suddivisi i ruoli?
Attualmente abbiamo un organico di circa 30-40 persone, compreso un ufficio dedicato all’acquisto dei metalli. Dall’arrivo del carico abbiamo uno staff solo al controllo conformità e qualità, per poi essere incanalato da addetti alla logistica alla corretta zona di carico o scarico. 11 mezzi permettono la movimentazione del rottame metallico, mentre una squadra interna di manutentori assicura la costante efficienza degli impianti di riciclaggio. Nella nuova sede si aggiungeranno due macchinari elettrici per il trattamento dei rifiuti, mentre la previsione per il personale è di implementarlo almeno a cento persone. Attualmente per l’impianto di riciclaggio Panizzolo sono dedicate 5 persone, mentre nella nuova sede aumenteranno.
Come è distribuita la vostra presenza tra Italia e Estero?
L’Italia resta sempre uno dei più importanti mercati di sbocco per la vendita del prodotto finito, economicamente pari all’ 80% del fatturato. A differenza l’acquisto del rottame metallico si suddivide a metà tra Italia ed estero. La vendita viene fatta solo ad acciaierie e trafilerie. Ad oggi le acciaierie e le trafilerie italiane sono il miglior bacino di vendita presente in Europa e sono sempre più esigenti sulla qualità del prodotto che acquistano. Esigenti sia rispetto al rapporto resa-fusione del prodotto che al consumo energetico. Evitano un prodotto non raffinato in modo ottimale perché crea costi supplementari di gestione e miscelazione nei forni, oltre al fatto che non rientra nei parametri di analisi interna.
Bisogna fornire alle acciaierie un prodotto che sia ritenuto qualitativamente buono da comprare. In caso contrario scatta la selezione naturale: o sei dentro ai loro parametri o sei fuori dalla lista di aziende da cui acquistano.
Per questo motivo in Com.Steel la qualità del prodotto è un fattore determinante su cui puntare.
Questa è anche la visione del prossimo futuro del mercato del rottame?
Assolutamente. Nella nuova sede che stiamo costruendo abbiamo messo a budget più di 4 milioni di euro per strutturare un impianto di riciclaggio completo di macinazione, raffinazione e selezione dei rottami metallici. Il cuore operativo è l’impianto di riciclaggio Panizzolo, fondamentale per macinare e ridurre il materiale ad una pezzatura perfetta per le attrezzature di selezione a valle.
Passiamo quindi al rapporto Com.Steel – Panizzolo e Com.Steel – macchinari Panizzolo.
Conosciamo Panizzolo da molto tempo ed eravamo vostri clienti fin da prima che iniziaste a vendere impianti di riciclaggio, quando esisteva solo la vostra attività di macinazione motori auto nella sede storica di Piove di Sacco. Da qui caricavamo una media di 2/3 autotreni al giorno di frantumato di ferro. Nel momento in cui Panizzolo ha iniziato a progettare e vendere soluzioni di riciclaggio, i modelli di mulini a martelli trasportabili sono stati talmente apprezzati da Com.Steel che abbiamo deciso di metterne giù uno ed iniziare anche il trattamento del barattolame con bada stagnata da RSU.
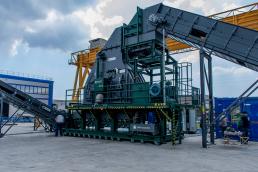
Perché all’epoca avete scelto Panizzolo come fornitore di impianti di riciclaggio?
Perché io e mio fratello siamo andati a vedere l’impianto di frantumazione a Piove di Sacco, quello con cui Panizziolo lavorava quotidianamente. Ci è piaciuto da subito perché era costruito con l’esperienza di chi ogni giorno lavora sugli impianti di riciclaggio. Tra il dire e il fare la differenza è parecchia.
Quindi l’esperienza diretta ha inciso fondamentalmente nella scelta di acquisto?
Assolutamente. I mulini a martelli Panizzolo posseggono determinati dettagli che solo l’occhio di chi ci lavora ogni giorno sa cogliere. Certi accorgimenti che nascono solo con l’esperienza diretta. Esempi possono essere molteplici: il rotore, la camera di macinazione e soprattutto la culla inserita nei mulini. Tutti plus che Panizzolo ha sempre saputo ribaltare sugli impianti che progetta e che vende.
Secondo lei culla intercambiabile brevettata è importante nella lavorazione del mulino a martelli?
La culla è fondamentale per il cambio veloce delle griglie in fase di manutenzione. Cosa che coincide con gli accorgimenti che nascono solo con l’esperienza diretta: la culla intercambiabile è fondamentale ma è decisivo anche il fatto che Panizzolo abbia progettato un macchinario semplice da manutenere, con un veloce accesso alla camera di macinazione. Effettivamente noi, che abbiamo un team interno dedicato solo alla manutenzione, teniamo sia culla che rotore doppi in modo da doverci fermare il minor tempo possibile. A lungo andare evitare questi tempi morti paga più che abbondantemente il fatto di avere dei doppioni a terra.
Questa velocità di manutenzione e sostituzione di culla e rotore hanno portato quindi dei benefici nel tempo?
Sì, sia in fase di manutenzione sia per i cambi di settaggio nel mulino a martelli. Con una macchina che lavora circa 10-11 ore al giorno ridurre notevolmente i tempi fermi di manutenzione si ripercuote in maniera importante nella produttività nel lungo periodo.
Però anche altre aziende del settore forniscono mulini con rotori intercambiabili.
Sì, però loro la culla non ce l’hanno e il cambio del rotore e delle altre componenti è strutturato in maniera completamente diversa. Molto più macchinosa.
Con l’avvio della lavorazione del primo mulino a martelli, è stata confermata la qualità che vi aspettavate?
Assolutamente. Oltretutto noi siamo già al terzo modello di mulino a martelli che acquistiamo da Panizzolo. Eravamo partiti con un Flex 1000 Mobile nel 2014. Poi siamo passati ad un Flex 1300 Mobile nel 2016, dove abbiamo aggiunto vari accessori di separazione. Nella nuova sede passeremo a maggio-giungo 2020 al mulino a martelli Mega 1500.
Cosa vi ha fatto riconfermare Panizzolo anche per il modello Mega 1500?
Chiaramente la scelta è stata fatta perché la linea di costruzione è stata mantenuta alla stessa qualità e professionalità delle stesse linee precedenti. Il mulino diventa più grande ma il concetto di come lavora è lo stesso, se non migliore. Per esempio il sistema di carico con piano oscillante. Sui precedenti modelli ci siamo trovati sempre bene, quindi non abbiamo nulla da temere sul prossimo modello.
All’inizio avevate scelto un impianto mobile, come mai questa preferenza?
I motivi sono tendenzialmente due. Il primo è che erano impianti di riciclaggio con potenza minore rispetto al Mega 1500. il secondo problema era lo spazio. Mentre nel nuovo sito avremo una zona dedicata al nuovo impianto di macinazione, nell’attuale sede avevamo troppo poco spazio per un impianto stazionario. La scelta quindi è ricaduta sui modelli mobili, compatti e completi di insonorizzazione, carico, trasporto e prima separazione.
Che produzione fate attualmente?
Oggi il barattolame con banda stagnata è il secondo prodotto che carichiamo in Com.Steel. Con l’attuale modello Flex 1300 Mobile andiamo dalle 60 alle 100 ton/giorno di caricato. A differenza di finito, a seconda di quanto è inquinato l’input, produciamo una media di 80 ton/giorno.
Dopo l’avviamento del nuovo mulino Mega, quali sono i programmi produttivi?
Il nuovo Mega 1500 verrà usato come sgrossatore, preparando il materiale per il Flex 1300 Mobile. La nostra esperienza nella lavorazione del materiale ci ha insegnato molte cose, tra cui la più importante è che un prodotto di qualità in output necessita dei giusti step di lavorazione. Non esistono macchine che fanno tutto in un unico passaggio, che siano rottami ingombranti o cavi elettrici. Non esiste perché alla fine perdi sia la produttività che la qualità. Nella nuova sede aumenteremo sicuramente il flusso di barattolame in entrata. Dalle circa 2 mila ton/mese che oggi facciamo di media, passeremo tranquillamente alle 4-5 mila. Tutto il gioco starà in come Com.Steel vorrà interfacciarsi con le griglie e un aiuto fondamentale arriverà dalla culla intercambiabile di Panizzolo sia del Mega 1500 che del Flex 1300 Mobile. Non abbiamo dubbi che potremmo contare su produttività di almeno 350 ton/giorno.
Potrebbe darmi maggiori informazioni sulla nuova sede?
Col passare degli anni l’attuale sede è diventata troppo piccola per i flussi di materiali. Giornalmente circolano 120 autotreni tra ingressi e uscita e circa 270 mila tonnellate annue di metallo trattato. Per questo motivo circa 3 anni fa abbiamo avviato un progetto di trasferimento in uno stabilimento più grande.
Nella nuova sede di 66 mila mq, cuore del ciclo di trattamento sarà l’impianto di macinazione Panizzolo.
Con il nuovo sito, oltre ad incrementare la produttività, potremmo ampliare il ventaglio di materiale trattato da Com.Steel. Un esempio è tutto quel rifiuto cascame prodotto da altri impianti di trattamento, ancora ricco di metalli e che al momento ha come unico sbocco la discarica. In quest’ottica non escludiamo la possibilità di installare un altro impianto, con un mulino a martelli sicuramente Panizzolo.
Cosa ne pensa dello slogan “è tempo di valorizzare al massimo i metalli”, introdotto da Panizzolo a Ecomondo 2019?
Sicuramente più che uno slogan è un obbligo, una mission che devono far proprie tutte le aziende del settore. Per continuare ad avere punti di sbocco dove vendere il prodotto le aziende devono intraprendere assolutamente questo percorso ilprima possibile. Le fonderie, acciaierie e trafilerie vorranno sempre maggiore qualità, mentre a causa della chiusura della Cina si è innalzata la richiesta in Europa e nel mondo di rifiuto da lavorare. Molti sperano nel fatto che presto la Cina riaprirà le porte, ma devono convincersi che lo farà solo per i semi-lavorati per le loro fonderie. Stessa questione per chi, ad oggi, cerca vie traverse in altri paesi orientali. Sono sbocchi che valgono per il tempo che valgono, instabili e fisiologicamente destinate a chiudersi.
Presso la nuova sede intraprenderete qualche politica ambientale?
Sicuramente. Anzi, stiamo agendo attivamente in questa direzione. Prima di tutto, per togliere la maggior quantità di traffico possibile, abbiamo costruito direttamente noi una nuova strada, lunga più di 1 km più, e un ponte sopra la ferrovia. Avendo un’importante flusso di materiale trattato annualmente, circoleranno circa 330 autotreni al giorno e non vogliamo che questo si ripercuota sulla vita della vicina città di Calusco d’Adda. Gli stessi autotreni avranno apposite zone di parcheggio aperte giorno e notte all’interno del nostro stabilimento, riducendo ulteriormente l’impatto sulla circolazione.
In secondo luogo stiamo installando un impianto fotovoltaico progettato per produrre circa 2 MegaWatt di energia, destinato al parziale utilizzo degli impianti di trattamento. Ovviamente la restante potenza necessaria verrà fornita da Enel che, come sappiamo, è il primo produttore italiano di energia da fonti rinnovabili.
Dal vostro punto di vista di esperti imprenditori del settore, quali consigli dareste alle aziende per affrontare il futuro?
Nel mondo del rottame metallico post duemila non c’è più spazio per il commercio per come l’abbiamo conosciuto. Il presente si muove verso la lavorazione e la raffinazione dei metalli. Le acciaierie andranno a saturare il mercato all’acquisto diretto del prodotto pronto forno, senza bisogno dei commercianti. Lavorare il materiale non vuole dire installare una cesoia o una pressa, ma bensì produrre un proler finito e arrivare fino a recuperare il più possibile lo scarto che esce dalla lavorazione per evitare il conferimento in discarica.
Meno discarica e più recupero?
Il meno possibile deve andare in discarica. Negli ultimi due anni, a causa anche del discorso Cina, il costo di conferimento si è quintuplicato. Le discariche stanno chiudendo e nei prossimi anni verranno completamente sostituite dai termovalorizzatori. Per esempio tutti gli scarti che Com.Steel produce dagli impianti di riciclaggio Panizzolo vanno conferiti completamente a termovalorizzatori. Quest’ultimi producono energia e calore, quindi andiamo ad alimentare un ciclo virtuoso.
Quali sono le fonti di informazione da cui attingete per il mercato?
Essere informati sulle ultime novità, oggi come non mai, è fondamentale per un’azienda del nostro settore. Noi siamo sia iscritti che sponsor di SiderWeb, principale piattaforma web per le novità del mercato metalli. Abbiamo continui rapporti con realtà che monitorano e pubblicano statistiche. Tuttavia fondamentale resta sempre parlare direttamente con i maggiori player come le accierie.
Come utilizzatore diretto, che consigli darebbe ad un’azienda che sta valutando l’acquisto di un impianto di macinazione come il mulino a martelli?
Vi sono molteplici punti di vista da analizzare. Prima di tutto la semplicità di manutenzione e sostituzione delle componenti soggette ad usura, tramite veloci accessi alla camera di macinazione. Poi la resistenza dei componenti, della cassa, del rotore e di tutti i componenti che intervengono alla lavorazione. Lavoriamo in un ambiente dove il mulino a martelli è soggetto ad importanti sollecitazioni ed è continuamente sottoposto ad urti. L’integrità di queste parti diventa fondamentale nel lungo periodo. Ovviamente il mulino non è fatto solo dalla camera di macinazione. È importante tutto quello che circonda la macchina: efficiente alimentazione, la trasmissione tra motore e rotore dove là ci deve essere dello studio e della tecnologia di qualità. Alla fine la semplicità deve venire prima di tutto: con manutenzioni semplici e rapide la macchina può restare in produzione più tempo possibile.
Il consiglio essenziale è di non cadere nella presunzione di voler fare tutto con un unico impianto di riciclaggio.
Non bisogna dar retta a quelle aziende che propongono queste soluzioni. Ogni prodotto necessita di adeguati martelli, griglie e calibrazioni. All’acquisto del primo mulino a martelli non avevamo ancora tanta esperienza, tuttavia Panizzolo ha saputo consigliarci con trasparenza quale fosse il miglior ciclo di trattamento. Una fiducia che gli abbiamo dato per la sua esperienza diretta e che ancora oggi è abbondantemente confermata. In tutti questi anni i mulini hanno lavorato senza problemi un materiale “bastardo” come il barattolame a banda stagnata.