Maximize the investment with Panizzolo Service
Panizzolo recycling solutions offer a wide range of industrial waste treatments with maximum flexibility of use. However, the composition of metal waste can cause our customers difficulties in regulating the treatment itself.
It ‘s therefore essential for the company to use the best after-sales tools, allowing a correct transfer of knowledge and the right balance between profitability, wear and energy costs.
Let’s talk about it with Mauro Bassan, Service Manager at Panizzolo Recycling Systems.
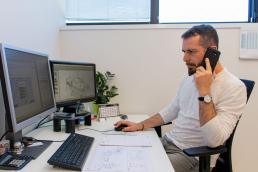
What are the goals of Panizzolo service? And how did you deal with the COVID-19 problem?
Remote assistance has enabled the after-sales services to be active at a time when direct interventions were not possible due to the COVID-19 pandemic, especially abroad. In recent weeks, however, we are also returning fully operational on this front.
Often we activate special web assistance channels for production consultancy, setting up the industrial waste treatment plant for new waste, maintenance, processing suggestions. Over the years we have outlined precise communication ethics with customers: professionalism, transparency in relationships and intellectual honesty.
In accordance with these objectives, the Panizzolo Recycling Systems service cannot focus only on the sale of spare parts. Our task is to lead the customer to full awareness of the production potential of the recycling plants he works with.
Can you better explain what you mean by remote service?
By appointment, it is possible to contact one of our technicians by telephone, LAN connection of the machine and new technologies available soon. With the remote service, or web, we give customers the opportunity to interface in a clear, simple and intuitive way. We can intervene to check the recycling machinery, inspections, general clarifications, 360-degree treatment suggestions and much more.
Let me explain through a practical example. A few days ago one of our customers contacted us asking for a couple of hours of advice to treat a new metal scrap because he wanted to find the best setting. I state that he is not new to the job, rather he has been working with our mobile mill for many years. He therefore sends us the photos of the metal waste, also explaining how he would have liked to set the grids to obtain a high quality output proler. Analyzing everything, we therefore corrected the configuration and parameters of the mobile mill, directing it to a more gradual and safer start. With the next appointment we will connect to the plc of the mill and complete the setting together, so that we can optimize it in real time.
It is not unusual for me to see that many customers, despite having their experience, continue to search for our advice. We even receive official thanks by emails for exceeding their production expectations
What can you tell us about original Panizzolo Recycling Systems spare parts?
Being both builders and direct users allow us to know exactly how metal castings and mechanical components will behave during processing. For this reason, Panizzolo original spare parts are designed to achieve always maximum production results.
There are cheaper options on the market, often improvised, which can lead to serious production problems. Our special melting hammers, for example, were developed together with the University of Padua both to guarantee constant quality and to eliminate the inherent problems of the more commercial models
In fact, we have found that some alloys risk abnormal wear or, worse, deformations of the structure which lead to important vibrations throughout the machine. Exactly a fact that one of our customers has experienced recently. This company, attracted by an affordable price, relied on a supplier who completely ignored the final field of use of the recycling machine. The inappropriate alloy consumed the hammers in a few weeks, deforming and locking them inside the rotor. Due to the vibrations, the hammer mill no longer guaranteed safe processing and we had to act promptly to avoid further negative consequences.
Are these peculiarities also found in other parts of the recycling machinery?
Absolutely. When you think of components subject to wear, you often imagine blades, hammers, armor or grids. However, grease also belongs to this category, especially the one used in rotor bearings. For the constant efficiency of the hammer mill it is essential to preserve the bearings over the long term.
In our recycling plant located in Piove di Sacco, we have tested different types of grease for high temperatures, choosing a special mixture in collaboration with a highly qualified Italian company. In comparison with other more commercial brands, it guarantees greater lubrication cycles, respects the integrity of the bearing in the long-term, reduces the operating temperature and, more importantly, does not fear metallic dust.
Just the other day I had the opportunity to discuss it with one of our customers. He wanted to find an alternative brand in his Country and was convinced that it would be enough to use the same grease applied in pellet mills and briquetting presses. However, I had to dissuade him from using it and explain to him that it would lead to problems with viscosity, heat point and mixing compatibility. Unfortunately, many people think that lubricating greases are all the same, which is absolutely wrong. Over the years I have been able to observe, also in other sectors, bearing breakages resulting from the lightness attributed to lubrication.
Are you planning any news in the near future? Can you tell us something?
As I told you at the beginning, during this year we will introduce implementations to the customer service. Come accennavo all’inizio, nel corso di quest’anno introdurremo delle implementazioni al servizio di assistenza. Obviously I can’t go into too much detail now, however I can anticipate something
In recent years, after-sales activities have seen an exponential increase in remote requests, customer interventions and spare parts sales.
We want to continue maintaining a high quality of service and at the same time remain consistent with our business goals. With this in mind, we are both investing in the internal organization and in the development of new technologies at the service of scrap treatment companies.
Remote assistance, starting from 2020, will be increasingly used and therefore we are completing the preparation of a new technology very useful for the customer and very simple to use. I can not say more, but in the coming months we will publish all the news of the Service Panizzolo.