CRL transforms and continues to grow with the new Panizzolo Recycling Systems plant
An active French company in the waste recovery sector, which boasts three treatment plants and considers the innovation of its processes as the pivotal point of its future. We interviewed Patrice Le Guern – owner of this family business – at the headquarters in the province of Bordeaux.
Good morning Patrice, can you tell us about your company?
CRL is a long-standing company in the waste recovery and recycling sector. It was founded in 1987 and subsequently – in 2001 – it was taken over by me and managed with the help of my brother and my son. From the acquisition to-date we have continued on an important path of growth that has led us to employ 25 people in three different sites – our headquarters in Saint-Emilion and two production plants in Countras and Toulouse – for an annual production of 40 tonnes.
We mainly process metal waste, such as scrap, sheet metal and ELV but also collection of copper, aluminium and stainless steel, which are then sold to refiners and foundries. In these processes, we have always invested in the modernisation and automation of activities. As part of this research, we first encountered Panizzolo through other companies and colleagues in the sector who already had some of your machines.
Why did you choose Panizzolo as a supplier?
After these first references, we wanted to visit the Panizzolo treatment plant in Piove di Sacco to personally evaluate its operations and tests. I must say that we were satisfied at the time and we are still satisfied with the plant that has been running for a few months.
The plant we purchased is a shredding line that allows us to optimise sorting and separate metals properly. These sorting activities were previously carried out visually and manually – therefore, slow and inconvenient – and did not allow for an effective subdivision of the treated materials. Now we can process our materials in all respects, treating ferrous metals above all adequately, and obtaining a selected, quality output product.
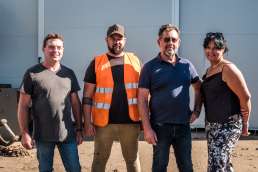
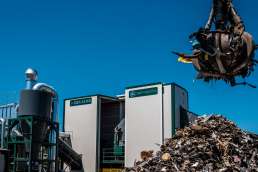
What are the technologies that make up the plant you installed?
The treatment plant we have chosen consists of a first step of volumetric reduction of the scrap with a shredder PZH 1500 R. Once the material has been processed, it is ready to be inserted into the grinding and selection cycle. This consists of a hammermill model Mega 1000 and various separation systems, such as eddy current, zig-zag and manual sorting cabins so as to separate ferrous, non-ferrous components and polluting aggregates, such as plastic, rubber, wood and even more.
What are the advantages of the plant and of this new way of working?
Certainly the transition from a manual to an automated process, which is really important to us. It allows us to save time and start processes in series and so we can define work days without hitches and machine downtime.
Among the advantages, the first aspect that we have all noticed is the silence: it does not produce any noise! The second aspect is the size: The hammermill is a very compact machine, which takes up little space, but it can optimally process significant amounts of scrap. The last aspect concerns the use: the personnel got used to it immediately because the operating logic and the management and control software are effective and simple.
What vision do you have for the future?
We plan to continue investing in the future. In this sense, we are already negotiating a second treatment line with Panizzolo Recycling Systems.
We do not want to limit our activity to the recovery of metal waste but we want to evolve towards a real transformation of the product and then, why not, set up a new metal treatment plant.
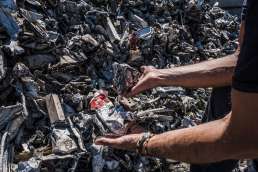
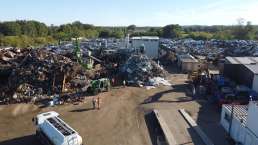
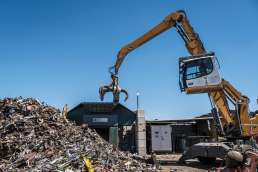