The overhaul quality of Panizzolo recycling machinery
Overhaul and regeneration of our used recycling machines: “In this phase we follow the same directives that we apply for testing new models.”
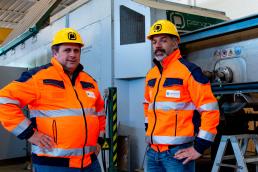
For the Panizzolo Recycling team, the return of a used recycling machinery is synonymous with new potential at the service of waste treatment companies, eager to develop their own business of grinding and refining metal scrap. For this reason, all our recycling machinery, including overhauled models, must comply with a quality policy aimed at maximizing the customer’s investment.
Today we show you how concretize this path, throught two used mobile mills recently returned after almost ten years of service and which will soon be operating again at two European companies. Sandro Tiozzo (Production Manager) and Denis Zanin (Electronics & Automation Manager) direct the team in charge of the interventions and they will explain to us what procedures they will apply.
How did you operate from the beginning with these two hammer mills?
Depending on what emerged in the operational briefing, the used recycled recycling machines can follow two processes: overhaul or regeneration. Today, for these two models, a special team of mechanics and electrical workers will carry out overhaul work. As soon as we returned we carried out a visual check both external and internal. We listed everything that needed to be replaced for both wear and integrity standards. The next step will be the complete mechanical and electrical disassembly.
How do you evaluate the element to be replaced?
We practically follow two logics. If during the check we detect components that are clearly worn, broken or malfunctioning, they are immediately reported and replaced with others of the same quality or higher. Depending on the case, we can also foresee a radical technological upgrade, as happened to the oledynamic unit of one of the two used hammer mills. Instead we follow a special procedure for those components subject to wear “borderline”.
In practice, our experience allows us to predict the behavior of the component in the near future and anticipate any production problems. It is therefore replaced in advance to avoid risks of this kind for the customer.
Let’s take a concrete example. When checking one of the used recycling machines we saw that a hood armor was worn but could still work. However, the years of grinding had consumed it in a particular way. We therefore analyzed how it would wear out in the near future and we decided to replace it because it would jeopardize production efficiency. These meticulous analysis phases are also guided by a consolidated company procedure, which guides us to the control of all the screws of the machine.
How do you proceed from the electrical and electronic point of view?
We are always evolving both from the software and electrical components point of view. It will therefore be physiological that the used recycling plants are not updated like the new ones. However, we always try to perform as many updates as possible, so that the revised models are in step with the new ones.
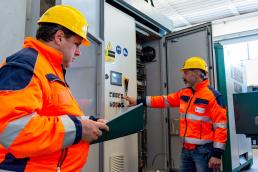
The two mobile mills used for example have about ten years of service behind them. We will proceed to implement many aspects such as remote assistance, proximity sensors, the safety circuit and much more.
In addition to the updates, we do extensive electrical checks. My team does not dwell on the non-functioning elements but rechecks all the components and wiring. The electrical panel is opened, cleaned from top to bottom and every component is inspected. In these two used and reconditioned recycling plants, the push-button panel for maintenance is a highly subject to wear. Consequently it will be dismantled, inspected and if necessary completely replaced. We will take particular care to update the management and control software. It is very important for the productivity of our recycling systems and our company continually invests to design updates. In one of the used mobile mill an operator terminal will be replaced while in the other the PLC will be updated.
Do you also proceed with the complete disassembly of the machinery?
Absolutely. The two hammer mills will be dismantled from a mechanical, hydraulic and electrical point of view. Mill, cradle, belts and rotor will be extracted, cleaned and examined to identify any anomalies. The rotor, the component more subject to grinding, is completely dismantled and overhauled. The bearings are examined, the balance is checked and then it is brought back to an optimal working condition. The oil is drained and replaced, while each tube and piston subjected to inspection. At the end of the works, everything is greased, lubricated and assembled again in its place.
Does it takes a long time for overhauls?
To do a job well done it always takes the right time. However our recycling machines have been designed for an easy maintenance. In this way my men are always able to perform the work in a very short time, safely and optimizing all operations. The patented cradle is the perfect example: once extracted, we can position it comfortably on the ground and have full access to the grinding chamber. Finally, Panizzolo hammer mills are solid and robust machines. These two models have worked for nearly ten years with electric motors, MSW and aluminum profiles. We cleaned and examined all the carpentry without finding any type of injury or crack.
How do you complete the review operatios?
Once mechanical and electrical work is finished, the recycling machines are assembled and tested here on site. In this phase my men will follow the same directives applied to the testing of the new models. We will perform all the mechanical and electrical tests scheduled before delivery to the customer, in order to avoid unexpected events or problems during installation and to ensure that our technicians concentrate as much as possible on operator training.