New Panizzolo strategies for post-emergency recovery
New Panizzolo strategies for post-emergency recovery
The exceptional situation caused by COVID-19 in recent months has changed many of our working habits with new logistical, health and production challenges. It therefore becomes essential to find new strategies to overcome the current emergency, given that coronavirus containment measures differ from country to country.
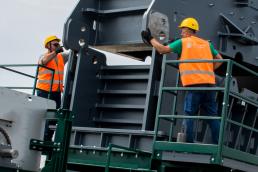
With a spirit of productive revival, Panizzolo Recycling Systems reopened its offices near Padua from 4th of May. In compliance with the Prime Ministerial Decree of 16 April 2020, we have previously prepared the recent national security protocol, informing and training all our collaborators, both to work in complete safety and to welcome all companies in the sector appropriately.
Together with our collaborators, we have chosen since March to continue production with the addition of adequate health measures. This continued until the national lockdown, without any impact on the health of our workers, carrying out the dense production planning and allowing us to reopen efficiently and safely in May.
During this period our service and sales offices remotely supported all the recycling companies, with the same efficiency and professionalism. In the same way, we reassured our collaborators by creating a special communication channel and publishing constant follow-up. To ensure the greatest possible protection, Panizzolo Recycling Systems has directly anticipated the extraordinary redundancy fund and shared a detailed production revitalization strategy, allowing us today to continue on the path of the set objectives.
We expect important changes in the scrap metal treatment sector in 2020, also thanks to the new action plan for the Circular Economy of the European Union.
To overcome this crisis, more and more recycling companies will focus on End-of-Waste treatment cycles, looking for suitable technological suppliers. In recent months Panizzolo Recycling Systems has worked on several fronts, developing its commercial skills and designing a new series of recycling machines that will soon be launched on the market. Consistent with our mission and vision, these new recycling technologies will allow companies to expand the production, logistics and quality performances of the secondary raw material output.
La qualité de révision des machines de recyclage Panizzolo
La qualité de révision des machines de recyclage Panizzolo
Révision et régénération de nos machines de recyclage usagées : « Au cours de cette phase, nous suivons les mêmes directives que celles que nous appliquons pour les tests des nouveaux modèles. »
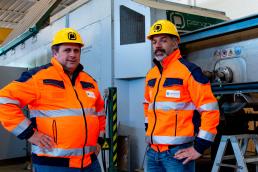
Pour l’équipe Panizzolo Recycling, le retour d’une machine de recyclage usagée est synonyme de nouveau potentiel au service des entreprises de traitement des déchets, désireuses de développer leur propre activité de broyage et d’affinage de ferraille métallique. C’est la raison pour laquelle toutes nos machines pour le recyclage, y compris les modèles révisés, doivent respecter une politique de qualité visant à maximiser l’investissement du client.
Aujourd’hui, nous vous montrons la manière dont nous concrétisons ce processus, à travers deux moulins mobiles usagés qui nous ont été retournés depuis peu, après près de dix ans de service, et qui seront bientôt de nouveau opérationnels dans deux entreprises européennes. Sandro Tiozzo (Responsable Production) et Denis Zanin (Responsable Électronique et Automatisation), qui dirigent l’équipe chargée des interventions, vont nous expliquer les procédures qu’ils vont appliquer.
Comment avez-vous procédé, depuis le début, avec ces deux moulins à marteaux ?
Selon ce que le briefing opérationnel a révélé, les machines de recyclage usagées qui nous été retournées peuvent suivre deux procédures : la révision ou la régénération. Aujourd’hui, pour ces deux modèles, une équipe spéciale de mécaniciens et d’électriciens va effectuer un travail de révision. Dès qu’elles nous ont été retournées, nous avons effectué un contrôle visuel externe et interne. Nous avons répertorié tout ce qu’il fallait remplacer aussi bien pour des raisons d’usure que pour les normes d’intégrité. La prochaine étape sera le démontage mécanique et électrique complet.
Comment évaluez-vous les éléments à remplacer ?
En somme, nous suivons deux logiques. Si, pendant le contrôle, nous détectons des composants manifestement usés, cassés ou défectueux, ils sont immédiatement signalés et remplacés par d’autres de même qualité ou d’une qualité supérieure. Selon les cas, nous pouvons également prévoir une remise en état technologique radicale, comme cela s’est produit pour l’unité de commande oléohydraulique de l’un des deux moulins à marteaux usagés. Nous suivons en revanche une procédure spéciale pour les composants soumis à une usure « limite ».
Dans la pratique, c’est notre expérience qui nous permet de prévoir le comportement du composant dans un futur proche et d'anticiper tout problème de production. Il est donc remplacé à l'avance pour éviter des risques de ce genre pour le client.
Prenons un exemple concret. En contrôlant l’une des machines de recyclage usagées, nous avons vu qu’une coque du capot était usée mais qu’elle pouvait encore fonctionner. Les années passées à broyer l’avaient toutefois usée d’une manière particulière. Nous avons donc analysé la manière dont elle se serait usée dans un avenir proche et nous avons décidé de la remplacer car son usure aurait compromis l’efficacité de la production. Ces phases d’analyse minutieuses sont guidées aussi par une procédure d’entreprise consolidée, qui nous guide jusqu’au contrôle de toutes les vis de la machine.
Comment procédez-vous du point de vue électrique et électronique ?
Nous sommes toujours en évolution constante tant du point de vue logiciel que des composants électriques. Il est donc physiologique que les installations de recyclage usagées ne soient pas mises à jour comme les neuves. Nous essayons toutefois de toujours effectuer autant de mises à jour que possible, de sorte que les modèles révisés aillent de pair avec les neufs.
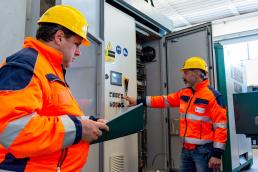
Les deux moulins mobiles usagés par exemple ont une dizaine d'années de service derrière eux. Nous procéderons à la mise en œuvre de nombreux aspects tels que l'assistance à distance, les capteurs de proximité, le circuit de sécurité et bien plus encore.
En plus des mises à jour, nous effectuons des contrôles électriques précis. Mon équipe ne s’attarde pas sur les éléments qui ne fonctionnent pas mais revérifie tous les composants et les câblages. Le panneau électrique est ouvert, nettoyé de fond en comble et chaque composant est inspecté. Dans ces deux installations de recyclage usagées et révisées, le boîtier à boutons-poussoirs pour la maintenance est un élément fortement soumis à usure. Il sera donc démonté, inspecté et complètement remplacé si nécessaire. Nous accorderons un soin particulier à la mise à jour du logiciel de gestion et de contrôle. Cela est très important pour la productivité de nos systèmes de recyclage et notre entreprise investit continuellement pour concevoir des mises à jour. Sur un moulin mobile usagé, un terminal opérateur sera remplacé, tandis que pour le deuxième, l’automate programmable sera mis à jour.
Procédez-vous aussi au démontage complet de la machine ?
Bien sûr. Les deux moulins à marteaux seront démontés d’un point de vue mécanique, oléohydraulique et électrique. Le moulin, le berceau, les bandes et le rotor seront extraits, nettoyés et examinés pour identifier toute anomalie. Le rotor, composant qui, de par sa nature, est plus soumis au broyage, est entièrement démonté et révisé. Les roulements sont examinés, l’équilibrage est vérifié ; le rotor est donc ramené à un état de fonctionnement optimal. L’huile est drainée et remplacée, tandis que tous les tubes et pistons sont soumis à inspection. À la fin des travaux, tout est graissé, lubrifié et remonté à sa place.
Les opérations de révision prennent-elles beaucoup de temps ?
Pour qu’un travail soit bien fait, il faut toujours lui consacrer le temps nécessaire. Nos machines pour le recyclage ont toutefois été conçues pour faciliter la maintenance. Mes hommes sont donc toujours en mesure d’effectuer le travail en très peu de temps, en toute sécurité et en optimisant toutes les opérations. Le berceau breveté en est l’exemple parfait : une fois extrait, nous pouvons le placer aisément au sol et nous avons un accès complet à la chambre de broyage. En fin de compte, les moulins à marteaux Panizzolo sont des machines solides et robustes. Ces deux modèles ont fonctionné près de dix ans avec des moteurs électriques, DSU et des profilés en aluminium. Nous avons nettoyé et examiné toute la charpenterie sans trouver aucun type de dommage ou de fissure.
Comment terminez-vous les opérations de révision ?
Une fois les travaux mécaniques et électriques terminés, les machines pour le recyclage sont assemblées et testées ici dans nos locaux. Au cours de cette phase, mes hommes suivront les mêmes directives que celles appliquées aux tests de mise en service des nouveaux modèles. Nous effectuerons tous les tests mécaniques et électriques programmés avant la livraison au client, afin d’éviter toute imprévue ou problématique lors de l’installation et de faire en sorte que nos techniciens se concentrent le plus possible sur la formation des opérateurs.
La véritable victoire finale, qu'il s’agisse d’installations de recyclage neuves ou usagées, est de faire comprendre aux personnes qui doivent les utiliser la manière exploiter correctement tout leur potentiel de production. Il n’y a que de cette manière que nous pouvons vraiment dire que nous avons atteint notre objectif.
GLOBAL RECYCLING DAY AND COLLABORATION WITH THE UNIVERSITY OF PADUA
GLOBAL RECYCLING DAY AND COLLABORATION WITH THE UNIVERSITY OF PADUA
The "Global Recycling Day" and “Earth Day” falls annually on march and april. The theme of this year are the "Recycling Heroes", that is, those people who every day contribute to a greener future for our planet. With these premises Panizzolo Recycling Systems has organized, thanks to the collaboration of Dr. Antonella Panizzolo, a specific web open day for the students of the study course "Techniques for the prevention of the environment and the workplace" of the University of Padua.
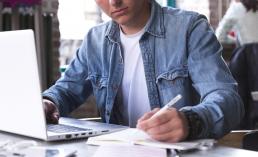
It is important for companies to bring more knowledge about work concreteness and provide students with greater professionalism in their future roles. We talk better about it with Dr. Antonella Panizzolo, professor of the course at the University of Padua.
With the recent emergency COVID-19 we had to modify the program for safety reasons, transforming it into an online lesson. Through videos and interviews we have shown why our company is certified in the production of second raw materials and how our End-of-Waste treatment cycle plants operate.
Could you give us a brief presentation of you, your study path and your career at the University of Padua?
I graduated in Prevention Techniques at the University of Padua and for 20 years I have been carrying out the activity of prevention technician at a public body where I deal with both the environment and safety in the workplace.
What are the objectives of the courses of study you direct?
From 2014 and up to the current academic year 2019/2020 I have been awarded a contract for the teaching of Environmental Verification and Control and Accident Prevention (Class: L / SNT4 – Prevention health professions) in the homonymous course enabling health profession of Prevention technician in the environment and in the workplace as per DM 58/97. The aforementioned Ministerial Decree establishing the figure of the Prevention Technician defines him as that health worker who, “in possession of the qualifying university diploma, is responsible, within the sphere of his own competences, for all prevention, verification and control activities in matters of hygiene and environmental safety in the places of life and work, hygiene of food and drinks, hygiene of public and veterinary health. The Prevention Technician carries out preliminary activities, aimed at issuing authorizations or technical health clearances for activities subject to control “.
As for teaching, the university course is divided into lectures, exercises and guided visits in the most significant recycling plants for the training of students such as landfills, purifiers, composting plants and waste management systems. Fundamental for students is the knowledge of environmental legislation which primarily includes the study of the single environmental text, D. Lgs.n. 152/06 and as amended with particular regard to part IV relating to waste, as well as the sector technical regulations, especially regarding recovery.
I believe it is important that students can acquire, in parallel with theoretical knowledge, the practical-technical applications and the founding principles of the prevention and protection of living and working environments and in this sense it is essential for them to be able to visit the recycling plants.
At the end of the study path, what are the roles that your students will play?
The degree course in Prevention Techniques prepares students to carry out future professional activities as “health professionals” both in the National Health Service – in the field of prevention, control and surveillance – and in the freelance regime.
The prevention technicians employed by the National Health Service or the Environment Agencies will be able to collaborate with the Judicial Administration for health and environmental investigations, carry out inspection and surveillance tasks and carry out controls in order to ascertain the authorization suitability as well as formulate opinions on irregularities detected while, in the private sector, they will be able to deal with consultancy in the field of Food Hygiene, Environmental Protection, Veterinary Public Health, Hygiene and Public Health or Safety in the Workplace.
Can you explain the importance of your initiative in accompanying your students to visit companies involved in waste treatment?
I consider it very important that students can see de visu what are the recovery activities that, starting from volumes of waste, allow to obtain raw materials as happens in the case of your company that deals with both the transformation from waste to resource and in parallel deals to produce hammermills for the enhancement of metals ready for sale on the market. Alongside the training activity in the recycling plant, the teaching program will analyze the authorization procedures to which companies dealing with waste recovery are subject.
The “Global Recycling Day” falls annually on March 18th. This year the theme will be “Recycling Heroes” to recognize the people who contribute most to the ecological future of our planet. In your opinion, will your students be the next Recycling Heroes? How?
In the world of youth there is much more awareness of environmental problems and critical issues than that of “adult” generations. Young people are demonstrating a strong interest in environmental issues from pollution to global warming and the movements of the Fridays for future for sustainable development and against climate change – which they see as the first activist Greta Thunberg – are a demonstration of this. In this sense, the students of this course also have all the qualifications to be Recycling Heroes candidates.
What do you think waste treatment companies should do to reduce the environmental impact?
In the European Union more than 2.5 billion tons of waste are produced every year and the EU is updating its waste legislation in order to promote the passage and development of the circular economy as an alternative to the current linear economy.
Companies in the sector often lack awareness and knowledge to put circular economy solutions into practice, other times investments in improving efficiency are not sufficient or are considered risky and complex. It is therefore appropriate, in my opinion, for companies to establish a relationship with university research centers.
CIRCULAR ECONOMY AND GREEN BUSINESS: WHAT'S NEW FROM THE EUROPEAN UNION FOR WASTE TREATMENT COMPANIES?
CIRCULAR ECONOMY AND GREEN BUSINESS: WHAT'S NEW FROM THE EUROPEAN UNION
FOR WASTE TREATMENT COMPANIES?
In case of activities that operate in the valorisation of waste and scrap, further help for economic recovery could come from the so-called "Green Finance".
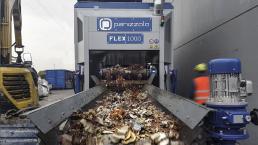
EU Commission President Von der Leyen in recent weeks has stressed maximum closeness to national governments, especially to Italy which represents a virtuous example in the management of the COVID-19 crisis. Economy remains a priority to be restarted, safeguarding companies and the labor market.
The next moves from Rome and Bruxelles will therefore be crucial to stabilize the markets and promote investments that are able to bring liquidity back to the corporate coffers. In case of activities that operate in the valorisation of waste and scrap, further help for economic recovery could come from the so-called “Green Finance”.
Born in 2007 with the launch of the first eco-bonds, the green business or Green Finance has the aim of financially supporting those projects that bring an advantage to the environment. After a slow start, there has been an increase in investors in the last decade and the consequent need for tighter controls. The European Commission is moving in this direction and, in the first months of 2020, it approved an action plan in favor of the Circular Economy.
Analyzing this document you immediately notice two strategies of fundamental importance. On the one hand, the regulation wants to disconnect economic growth with the extraction of new raw materials and consequently promote End-of-Waste recycling cycles. In doing so, the EU aims to keep resources within the economic circuit as much as possible and implements the appeal launched by the BIR during the last congress in Budapest. The regulation currently includes product categories such as household appliances, electronics and end-of-life vehicles, with the possibility of widening the scope.
Another point of the approved document is the “green taxonomy” to classify which financial investments can bear the “sustainable” label. Taxonomy is the fundamental basis in the green business regulatory package. It will allow to create a common language for investors and will allow environmental scores to be given to projects.
With this action plan, we want to direct greater capital flows towards green investments. Clearer rules, transparency and credibility will be the trump cards to incentivize investors and avoid the risk of greenwashing (i.e. a fraudulent method that uses ecology only as a facade).
This plan was approved in early March and scheduled enough long times to take effect. However, COVID-19 emergency, that is passing through Europe in recent weeks, has radically changed priorities.
Today the greatest challenge is to find the right stimuli to restart the economy. The recent regulation for the Circular Economy could become, if implemented in a short time, a source of economic recovery for waste treatment companies. The future of the sector, as pointed out both by the BIR and our company, lies in the complete valorisation of waste and reintroduction of second raw material into the production cycle. It will therefore be necessary for the EU to review the implementation agenda in order to concretize the plan as soon as possible.
INTERVIEW WITH MR. SCHUSTER
INTERVIEW WITH MR. SCHUSTER
ENHANCEMENT OF THE GERMAN ALUMINIUM SCRAP WITH PANIZZOLO HAMMER MILLS
Schuster Metall-Recycling GmbH is headquartered in Wemding, Germany. Located about halfway between Munich and Frankfurt, it has worked for many years in the treatment of various types of waste, with a specialization in the aluminium profile. Mr Schuster‘s technical and engineering experience, combined with practical knowledge of the world of scrap trading, allows him to choose the correct machinery to get the most from metals and confer them directly to German foundries.
Who is Mr Schuster? What about the Company and his history?
Founded by my father and now run by me, we started fifty years ago with simple world of scrap trading. Over the years we have decided to specialize in metal treatment. We have installed recycling systems and consequently increased our presence in the German and foreign market. Today the company sells more than 3000 tons per month of second raw material that we directly deliver to the foundry. More or less the sales are distributed around 60% in Germany and 40% in European countries.
What makes us different in the German market today is the efficiency of the recycling plants we work with, the high quality output, professionalism in relationships and flexibility of treatment.
Where does your technical knowledge of treatment plants come from?
I learned on my own. Processing the material and seeing what you can do with it.
I work with lots of machines and I have to understand what I want to obtain from each machine. The most of machines that I bought are still working on my plant. My next goal is very hard, but I want to improve the output quality. In this moment it is not easy to find a good material, it depends on price. There is no scrap in market, due to car crisis.
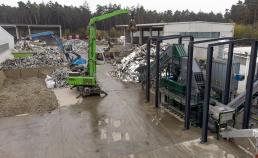
Do you think that German and Italian scrap companies are similar?
Yes, they are similar. We treat a wide range of metal scrap but we specialize in aluminium. For this reason, many times we market with foreign countries, including Italy. In general, the German market has a slightly higher metal quality than other countries.
What type of recycling plants do you work with? Where do you deliver their outputs?
In our company there are cable treatment plants, presses, shredders, separation systems and a Panizzolo Mega 1100 hammermill. For the most part the outputs produced, are supplied in national foundries and also in countries such as Italy, Austria and Poland. For example, the Panizzolo Mega 1100 hammermill mainly works with an aluminium profile, the output of which is transformed by the German foundries into raw materials mainly for the automotive market.
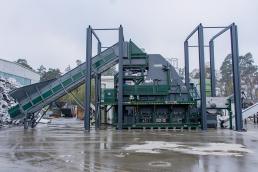
Why did you decide to use a hammermill?
Because the Mega 1100 hammermill allows us to obtain a perfect aluminum quality for direct transfer to the foundry. For example, a shredder would never allow us to achieve this goal. All European foundries, and especially German foundries, demand ever greater quality from the material they buy. There is quality and quality of aluminum. For example, Italian foundries want an aluminium quality different from ours because they have other outlet markets. However, the quality standards are growing day by day.
Why did you choose Panizzolo hammermills?
Because Panizzolo recycling solutions are simple to use, they are not huge machines and are very strong. Totally suited to my needs. The first hammermill I purchased from Panizzolo was Flex 1000 Mobile drum. It was one of the first hammermills I used, so I had to weigh the investment well. The machinery has lived up to expectations and has worked for almost ten years with an average production of about 6 tons/h. Currently from the new Mega 1100 hammermill I get an output production of 12 tons/h. I think that I will also easily reach at 15 tons/h, as it is working 70% of its potential.
What do you think of the interchangeable cradle in our hammermills?
It is an excellent idea and another factor of uniqueness that made me choose working with you.
The aluminium profile that I buy is not always the same and the cradle guarantees me flexibility and setting speed in the Mega 1100. Maintenance is simple, safe and quick, allowing to reduce all downtimes. Furthermore, in the near future it will allow me to perform fast treatment tests on other kinds of waste.
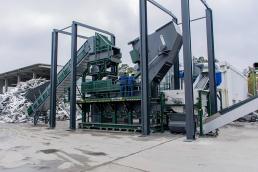
Other pluses that you found in the Panizzolo mill?
In general I like the whole construction logic. You can immediately see that the design is the result of years of direct experience in the sector. I myself have created my baggage of technical experience by operating directly. Mauro Panizzolo and I have the same vision of what is technically needed in a machine to work better. Concrete example are the hammers in special casting, born from a study in partnership with University of Padua. When I tested them I saw a radical difference in the wear and the quality of outputs.
Have there been any changes in the German scrap market in recent years? What future lies ahead in this sector in Germany?
Certainly in recent years there have been important changes, due both to internal and external factors. In Germany, the crisis in the automotive sector caused a drop in the purchase of foundries. The closure of China allows us to keep more scrap within our borders but we are experiencing a shortage in quality.
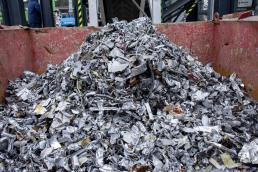
The future of the sector will focus on the treatment of scrap and the enhancement of metals.
When China reopens import, it will be only for semi-finished products and Germany is a nation that needs excellent quality raw materials for its products. It therefore makes no sense to continue marketing scrap as it is. One of our major strengths is the quality of the output metals. The combination of my technical and commercial experience and the use of Panizzolo machinery will be the winning weapon for the next few years to come.
What advice would you give to German companies that would like to install a treatment plant?
Unfortunately there are no big shortcuts. You must be clear in what you want to achieve at the end of the production process. You must always keep up with what market requires and build your own baggage of experiences, as I did. Finding a trusted technology supplier is not easy and unfortunately many pretend to be what they are not. Fortunately, I found in Panizzolo a valid partner who designs excellent machinery and which allows me to maximize the enhancement of the metals I sell.
WHICH MEASURES ARE LAUNCHED TO PROTECT THE ECONOMY?
WHICH MEASURES ARE LAUNCHED TO PROTECT THE ECONOMY?
The COVID-19 emergency has brought fear and uncertainty both on the personal health front and on the stability of markets and companies. Today it is difficult to estimate the consequences, but governments are acting to limit the negative effects.
Panizzolo Recycling Systems communicates its closeness to all collaborators, employees, customers and suppliers. A recent article in Il Sole 24 ore underlines how the new coronavirus is paralyzing the world economy as only the 2007-2008 economic crisis had been able to do. If not even more.
Alongside the climate of general concern, however, some news of the past weeks speculated a new miracle at hand. Europe, which until recently seemed to focus on the health of the population only, is realizing that in the near future the effects could be those of a war economy. Therefore, extraordinary actions are needed to face extraordinary events.
After a first moment of tension linked to the crazy sale of securities, the intervention of states and central banks gave relief to European finance. Fundamental contributions were made by the ECB president with a bank credit plan for SMEs, while Brussels de facto suspended the Stability Pact for all European countries. Investors also liked the maneuver of the Italian government which, on Monday 16 March, allocated 25 billion euros with the Cura Italia Decree. Companies are thus suspended from tax compliance, payments from public administrations and other subsidies to employees. A cure-all for Piazza Affari, which is slowly rising.
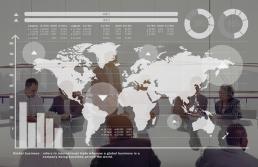
But what will change for us?
The day will come when the health crisis will be over and slowly we should get up in a totally different economy, where logics that previously seemed indisputable have been disrupted.
In our sector, the most positive forecasts concern the business of services and raw materials. By aiming to maximize the enhancement of metals, they will be more likely to get up first and revive the Circular Economy with greater momentum. Governments are moving in that direction and Panizzolo Recycling Systems is also trying to do its part by offering high quality recycling packages that can better optimize companies’ investment. It is said that “it is getting darker before dawn.” Who knows, maybe we are on the eve of a new economic miracle?
COVID-19: LEAVE VIRUS OUT
COVID-19: LEAVE VIRUS OUT
Dear customers,
The Italian Council of Ministers issued a further decree to fight the spread of Covid-19. With a special decree, therefore, non-essential work is suspended throughout the Italian peninsula. We pause our physical locations and we continue, where possibile, with smart working. All Panizzolo team gave their maximum support to continue their work remotely. We garantee that we will respond to ALL requests giving priority to the most urgent ones.
We trust in your support in overcoming this difficult moment.
We will keep you updated on the evolution of the situation.
Thanks from all Panizzolo team.
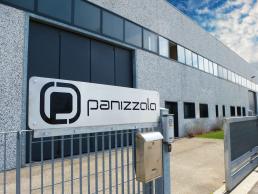
ETHICAL COMPETITION: ACCEPTANCE OF THE PANIZZOLO APPEAL
ETHICAL COMPETITION: ACCEPTANCE OF THE PANIZZOLO APPEAL
The competition stimulates Companies to provide goods and services more and more innovate. However, when entrepreneurs fail professional correctness , the disadvantage lies one customers.
The nobel prize in literature 1949 William Faulkner wrote: "It's competition that keeps the world moving, not love."
Historically, competition and concurrency brought many benefits to society. For example the tight race to the moon between the United States and the Soviet Union had important positive effects in the fields of medicine, telecommunications and civil engineering.
In the same way, in the modern market, the comparison between companies is of vital importance. To protect the profitability of our customers investment, Panizzolo Recycling invests in Research & Development and maintains a high commercial ethics with all companies in the sector of metal waste treatment. Panizzolo recycling solutions represent years of knowledge, whose concrete quality is recognized both by customers and competitors. That’s good to be encouraged by competitors so we can emprove everyday.
But what happens when professional correctness ceases and some companies start to abuse this right? Depending on the case, dangerous behaviors may be initiated such as, for example, acts of confusion (imitation), acts of denigration, dumping and more. Obviously each singular case has to be examined in the appropriate place, where the jurisprudence protects those who have the right.
In the meantime, who is the real victim? It is the end customer. Without correct comparison parameters end consumer’s choice can be influenced by distorted and not healthy trends of competition. When business ethic fails, what remains after all?
We are aware to have unique and innovative products and we watch over the market to ensure that healthy competition protects all our customers.
Recently, Panizzolo has been involved in a litigation with an Italian Company responsible of infringements for unfair competition and violation of trade secrets.
The Court of Venice with supervision order published in february 24 th , 2020 with R.G.8435/2018, recognized that documents on which legal protection was requested, had economic value and could bring to competitive advantages on the market. Therefore, in the outcome of the procedure, with decision that can be modified in the next judgments stages, the Court recognizes that “It is clear that its technical and commercial know-how has been taken from the applicant (Panizzolo, ndr) and it has been used by the defendant”, and “Inhibitory must be granted in order to prevent the defendant from using confidential information, which can lead to an illegal competitive advantage (…):
“For these reasons
Order to the defendant [name] not to use the confidential information pertaining to the applicant [Panizzolo, ed.] and subject of the description provision”
This decision from the Court of Venice leads us to continue and strengthen our market surveillance activity. We are recognized for the high quality of our recycling solutions. For this reason our clients must be able to choose the best solutions for their business activities.
COVID-19 Emergency: PANIZZOLO DOES NOT STOP
COVID-19 Emergency: PANIZZOLO DOES NOT STOP
“Dear Customers,
Given the continuing health alarm relating to COVID-19, we wish to update and to reassure you about the situation in our area and in our company.
Panizzolo Recycling Systems continues its production activities at full capacity, confident that the alert situation could be resolved as soon as possibile.
The company has adopted adequate measures, in accordance with the Decalogue published by the Italian Institute of Health, to ensure the health of its employees. Fortunately, to date there are no problems of any kind.
The activities therefore are regularly provided to guarantee the usual service levels.
We trust in our support and we believe that our commitment could help the sector and the whole country in overcoming this moment of difficulty.
We will keep you updated on the evolution of the situation. Our officies are at your disposal for any information.
Thanks from all the Panizzolo team”
Let’s start a new cycle of interviews by Panizzolo: Andrea Pensotti Com.Steel
Let’s start a new cycle of interviews by Panizzolo: Andrea Pensotti Com.Steel
Let’s start a new cycle of interviews by Panizzolo.
The first interviewed is Andrea Pensotti, owner and business partner of Com.Steel Spa.
The company is leader in metal and ferrous scrap sector with commercial relationships all over the world. Com.Steel Spa proposes itself as a partner of companies that operate with reliability, professionalism and with respect for the environment. It currently processes and trades all the main categories of metal and ferrous waste.

How was Com.Steel born and how are you working today? Could you tell us about yourself and the company?
Com.Steel was born about 30 years ago from my dad, my brother Edoardo and me. Edoardo manages the whole commercial and production phase while I follow the environmentall and administrative part. For the first 10-15 years we focused on the treatment of electrical cables, with a production of 50-60 ton/day.
Over the years we have decided to diversify the treated material, thus going to touch all various sectors. For the first 14 years, the headquarters were located in the province of Lecco, on a site of about 5 thousand square meters. When we began to diversify and develop the various treatment sectors, the need for more space to manage flows and logistics arose. We, therefore, moved in 2003 to the current headquarters, in Calusco D’Adda, in a space of 20 thousand square meters. In this way, we have managed to further develop the various types of metal scrap, specializing in the world of stainless steel. In recent years we started working with the largest Italian and European steel mills.
Today and future goal of Com.Steel is to treat as many categories of scrap metal as possible and to maximize the enhancement of the contained metals. This allows to be not dominated by the market and to divide the business risk. These peculiarities allowed us to establish ourselves as the main player in the Italian and world market in the purchase and sale of scrap metal; also for this, for three years, we have been working on the construction of the new headquarters.
Could you tell me about your company staff? How many are you and how are the roles divided?
We currently have a staff of around 30-40 people, including an office dedicated to the purchase of metals. At the entrance of the plant our staff checks the compliance and the quality of the material. Then this material is channeled by logistics personnel to the correct loading or unloading area. 11 means allow the handling of the metal scrap, while an internal team of maintenance workers ensures the constant efficiency of the recycling plants. In the new headquarters we will add two electrical machinery for waste treatment, while the forecast for staff is to implement it at least one hundred people. Today 5 people are dedicated to the Panizzolo recycling plant, but they will increase.
How is your presence distributed between Italy and abroad?
Italy always remains one of the most important outlet markets for sale of finished product, economically equal to 80% of the turnover. Unlike the purchase of scrap metal, it is divided in half between Italy and abroad. The sale is only to steel mills and wire drawing mills. Today, Italian steel mills and wire drawing mills are the best sales area in Europe and they are increasingly demanding on the quality of the product they purchase. They are demanding both in terms of product yield-melting ratio and energy consumption. They avoid an unrefined product in an optimal way because it creates additional management and mixing costs in the ovens, in addition to the fact that it does not fall within the internal analysis parameters.
It is necessary to supply the steel mills with a product qualitatively good to buy. If not, natural selection starts: either you are within their parameters or you are off the list of companies from which they buy.
For this reason, in Com.Steel the quality of the product is a determining factor to focus on.
Is this also the vision for the near future of the scrap market?
Absolutely. In the new site that we are building, we have budgeted more than € 4 million to structure a recycling plant complete with grinding, refining and selection of scrap metal. The operating heart is the Panizzolo recycling plant, that is essential for grinding and reducing the material to a perfect size for downstream selection equipment.
Let’s move on to the relationship: Com.Steel – Panizzolo and Com.Steel – Panizzolo machinery.
We have known Panizzolo for a long time and we have been your customers since before you started selling recycling plants, when there was only your car engine grinding activity in the historic headquarters of Piove di Sacco. From here we loaded an average of 2/3 truckloads of crushed iron a day. When Panizzolo started to design and sell recycling solutions, the models of transportable hammermills were so appreciated by Com.Steel that we decided to install one and start treating the tinplate cans from MSW.
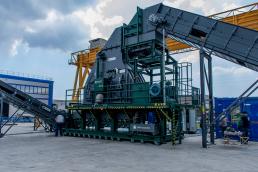
Why did you choose Panizzolo as your recycling plant supplier at the time?
Because my brother and I went to see the crushing plant in Piove di Sacco, the one with which Panizzolo worked daily. We liked it immediately because it was built with the experience of those who work on recycling plants every day. There is a lot of difference between saying and doing.
So direct experience has fundamentally affected the purchase decision?
Absolutely. Panizzolo hammermills have certain details that only the eye of those who work there every day can grasp. Certain precautions that arise only with direct experience. For example: the rotor, the grinding chamber and above all the cradle inserted in the mills. All pluses that Panizzolo has always been able to overturn on the systems it designs and sells.
In your opinion, is this patented interchangeable cradle important in the working of the hammermill?
The cradle is essential for a quick change of the grids during maintenance. These precautions arise only with direct experience: the interchangeable cradle is fundamental; but the fact that Panizzolo has designed a machine that is simple to maintain, with quick access to the grinding chamber is also decisive. We have an internal team dedicated only to maintenance. We keep double cradle and double rotor in order to stop the line as little time as possible. In the long run, avoiding these downtimes also pays for having spare parts in addition.
Did this speed of maintenance and replacement of the cradle and rotor bring benefits over time?
Yes, both during maintenance and for setting changes in the hammermill. With a machine that works about 10-11 hours a day, reduce maintenance downtime has an important impact on productivity.
However, there are other companies in the sector that supply mills with interchangeable rotors.
Yes, but they don’t have the cradle and the change of the rotor and other components is structured in a completely different way. Much more cumbersome.
Working with the first hammermill, has the quality you expected been confirmed?
Absolutely. Besides, for us it is already the third hammermill model that we buy from Panizzolo. We started with a Flex 1000 Mobile in 2014. Then we moved on to a Flex 1300 Mobile in 2016, adding various separation accessories. In the new headquarters, in May-June 2020, we will move on to the Mega 1500 hammermill.
What made you reconfirm Panizzolo also for the Mega 1500 model?
Clearly the choice was due to the construction line. It was maintained at the same quality and professionalism as the previous lines. The mill is bigger but the concept of how it works is the same, if not better. For example the loading system with oscillating table. We have appreciated the previous models, so we have nothing to fear on the next model.
At the beginning you had chosen a mobile system, why this preference?
The reasons were basically two. The first was that they were recycling plants with less required power than Mega 1500. The second problem was space. While in the new site we will have an area dedicated to the new grinding plant, in the current location we had too little space for a stationary plant. The choice therefore fell on the mobile models, compact and complete with soundproofing, loading, transport and first separation.
What is your production?
Today tinplate cans is the second product we load in Com.Steel. With the current Flex 1300 Mobile model we load from 60 to 100 tons/day. Regarding the finished product it depends on how much polluted input meterial is. We produce an average of 80 tons/day.
After the start of the new Mega mill, what are the production plans?
The new Mega 1500 will be used as a roughing machine, preparing the material for the Flex 1300 Mobile. Our experience in material processing taught us many things, the most important of which is that a quality product in output needs the right processing steps. There are no machines that could do everything in one step, whether they are bulky scrap or electric cables. It doesn’t exist because in the end you lose both productivity and quality. In the new location we will certainly increase the flow of incoming cans. From the approximately 2,000 tons / month that we do on average today, we will reach quietly to 4-5 thousand. The whole game will be in how Com.Steel will want to interface with the grids and a fundamental help will come from the interchangeable cradle of Panizzolo of both Mega 1500 and Flex 1300 Mobile. We have no doubt that we could count on productivity of at least 350 tons / day.
Could you give me more information about the new location?
Over the years, the current location has become too small for material flows. Every day 120 lorries circulate between inputs and outputs and about 270 thousand tons of treated metal per day. For this reason, about 3 years ago we started a relocation project to a larger plant.
In the new 66,000 m2 site, the heart of the treatment cycle will be the Panizzolo grinding plant.
With the new site, in addition to increasing productivity, we could expand the range of material treated by Com.Steel. An example is the enhancement of waste produced by other treatment plants. It is still rich in metals and currently it has the landfill as only outlet. With this in mind, we do not rule out the possibility of installing another system, with a Panizzolo hammermill.
What do you think of the slogan “it’s time to maximize the value of metals”, introduced by Panizzolo at Ecomondo 2019?
Certainly, it is more than a slogan, it is an obligation. It is a mission that all companies in the sector should pursue. To continue to have outlet points where selling the product, companies must absolutely follow this path as soon as possible. Foundries, steel mills and wire drawing mills will always want more quality, while the demand in Europe and in the world for waste to be processed has increased, due to the closure of China. Many hope that China will soon reopen its doors, but they will only do it for the semi-finished products for their foundries. The same question for those who, today, are looking for cross roads in other eastern countries. These outlets are valid for the time they are worth, they are unstable and physiologically destined to close.
At the new location will you undertake any environmental policy?
Definitely. Indeed, we are actively acting in this direction. First of all, to take away as much traffic as possible, we built a new road directly, more than 1 km long, and a bridge over the railway. Having an important flow of material treated annually, about 330 road trains will circulate per day and we do not want this to affect the life of the nearby city of Calusco d’Adda. The same trucks will have special parking areas open day and night inside our factory, further reducing the impact on traffic.
Secondly, we are installing a photovoltaic system designed to produce about 2 MegaWatts of energy, intended for the partial use of the treatment plants. Obviously, the remaining necessary power will be supplied by Enel which, as we know, is the first Italian producer of energy from renewable sources.
From your point of view of expert entrepreneurs in the sector, what advice would you give to companies to face the future?
In the world of post-2000 metal scrap there is no room for commerce as we have known it. The present moves towards the processing and refining of metals. The steel mills will saturate the market with the direct purchase of the oven ready product, without the need for merchants. Working the material does not mean installing a shears or a press, but rather producing a finished proler and going as far as possible to recover the waste that comes out of the processing to avoid the landfilling.
Less landfill and more recovery?
As little as possible must go to landfill. In the last two years, also because of the China speech, the cost of transfer has increased fivefold. Landfills are closing and will be completely replaced by waste-to-energy plants in the coming years. For example, all the waste that Com.Steel produces from Panizzolo recycling plants must be completely transferred to waste-to-energy plants. The latter produce energy and heat, so let’s feed a virtuous cycle.
What are the sources of information you draw from for the market?
Being informed about the latest news, today as never before, it is essential for a company in our sector. We are both members and sponsors of SiderWeb, the main web platform for metal market news. We have continuous relationships with companies that monitor and publish statistics. However, it is still essential to speak directly with the major players such as the steel mills.
As a direct user, what advice would you give to a company that is considering purchasing a grinding plant such as a hammermill?
There are multiple points of view to analyze. First of all, the simplicity of maintenance and replacement of components subject to wear, through quick access to the grinding chamber. Then the resistance of the components, the case, the rotor and all the components involved in the processing. We work in an environment where the hammermill is subject to important stresses and is continuously subjected to impacts. The integrity of these parts becomes fundamental in the long run. Obviously the mill is not made only by the grinding chamber. Everything that surrounds the machine is important: efficient feeding, the transmission between the motor and the rotor where there must be quality study and technology. In the end, simplicity must come first: with simple and rapid maintenance, the machine can remain in production for as long as possible.
The essential advice is not to fall into the presumption of wanting to do everything with a single recycling plant.
We must not listen to those companies that offer these solutions. Each product requires adequate hammers, grids and calibrations. When purchasing the first hammermill, we did not have much experience yet, however Panizzolo was able to advise us transparently about which was the best treatment cycle. A trust that we have given him for his direct experience and which is still abundantly confirmed today. In all these years the mills have worked without problems a very difficult material such as tinplate cans.