The new challenges in the industry, between diversification of the processed metals and a recovery of secondary quality raw materials
In a new interview with Andrea Pensotti, member and owner of Com.Steel Spa, we do a report of the year just ended, characterised by the pandemic, and we analyse outlooks for 2021 which will witness important changes in the sector.
We left our old headquarters in January 2020. Now, what has changed after a tough year due to the Covid-19 health emergency?
Fortunately, the pandemic had the direct effect of only postponing our transfer to the new headquarters by three months. By directly completing 2 km of road construction and of the bridge above the railway, we detoured truck traffic away from the city centre, a regulatory obligation required for the release of the new authorisation. Thereby the new 66,000 m² plant was inaugurated on January 11, 2021, and, at the same time, all of the tests on the new Panizzolo Mega 1500 hammermill were completed, today fully in service.
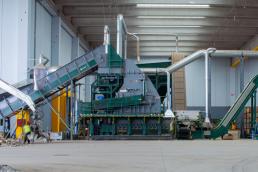
Changes on the market in the second semester of 2020 brought about important variations in the demand and supply of scrap. We focused on other types of incoming metals, without prejudice to our objective of tripling the production quantity of the processed materials. We simply reset our timetable. We currently work with a production capacity of 50%, but which will be increased to 80% by the end of the year.
Speaking more in general, our sector was not particularly affected by the pandemic. 2020 started very positively and, despite two months of practically total stop, we only recorded a -3% deficit at the end of the year.
If we more specifically analyse the scrap sector, we will definitely notice a great difference between those who processed and those who only marketed. The real winners were those who were able to differentiate their recycling cycle and can get going again today with a strong advantage, especially as far as investments are concerned.
How did 2021 begin?
Entering 2021, the demand for raw materials has skyrocketed. Last year’s drop in production is giving way to a gradual recovery of companies. Therefore the demand is in constant increase, but certain types of scrap are starting to be lacking. Ours is a particular sector: we suffer both the negative and positive consequences later than the rest of the market. This is why flexibility is more than ever the keyword today, valorising those scraps that are easiest to find.
So what are your goals?
We want to be ever more focused on the treatment of metals and on the diversification of the processed materials. This is also why we immediately started the new Panizzolo grinding and sorting plant in January.
The more we work, the more we understand that steelworks want a refined product. Quality is an element that is ever more awarded and looked for, while low efficiency products, polluted or contaminated by other metals, are becoming materials that the buyer has ever less interest in.
This is why in 2021, the new Panizzolo plant will mainly be focused on the treatment of tins from MSW, already ideally tested in the recovery of ferrous proler and in the separation of inert fractions. In April we will finish the revamping of the Flex 1300 Mobile drum mill, incorporating it in line with the Panizzolo plant and allowing us to obtain better quality proler. It will be cleaner and thicker, ideal for Italian and European steelworks.
As we already said, for us nothing ends up in a landfill. The separation systems upstream of the Mega 1500 allow us to recover many inert fractions. Glass dust, for example, is resold to produce new containers while the inert pieces are sent to waste to energy processing plants, thus creating a continuous production cycle.
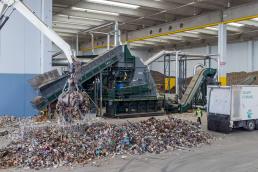
Speaking of the new Panizzolo plant for the treatment of tins, how was its processing logic studied? Do the initial results satisfy you?
Thanks to the experience gained in the use of previous Panizzolo machinery, together with our technical department, we’ve perfected the plant inside our new areas, allowing us to perform a complete and non-stop treatment.
Our operators have been instructed and trained regarding the various processing stages and now, to complete the test stages, we’re working with Panizzolo technicians on programming. Indeed optimisation of the hammermill software is fundamental and all of the necessary changes must be made for the correct setting of the machine.
As far as wear, maintenance and use are concerned, the Panizzolo Flex 1300 hammermill was a guarantee. We expect the same from the new Mega 1500, especially because in the first two months of processing the only thing that we’ve done, besides inspections and routine greasing operations, was to invert the working direction of the hammers.
We are satisfied with the collaboration with Panizzolo and its staff as everything was done according to the state-of-the-art. We’ve known Panizzolo for decades and their dedicated service technicians are as trustworthy as can be.
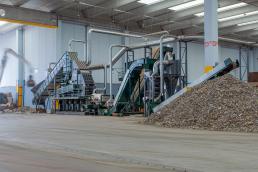
Do you have any information on incoming tins?
The tins come both from Italy and abroad, for an incoming volume of approximately 2000 tons a month. The hammermill works at a continuous cycle to keep the production quantities high. Market prices are currently very high and this material is easy to find.
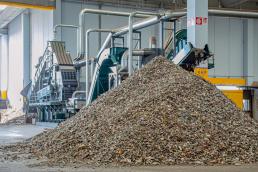
What will be your challenges in 2021 and in the coming years?
It will mainly be the need of installing ever more sophisticated plants to remain in the forefront. Not very many are going in this direction. Companies are afraid of the emergency situation and find it difficult to make an investment plan for the near future. Nonetheless, to get restarted we need to diversify production and to work on the quality of the finished product.
At Com.Steel, starting up new technologies will definitely be a topic for discussion in our 2022/2023 budget. We are actually very pleased with the Panizzolo lines that we are using and so we hope to keep working with them even for the installation of a future refining line.