Interview with Richard Groß, general manager of PIP Processing In Plastics
Next to the well-known scrap treatment companies there are highly specialized industrial realities. They do not treat aluminum profiles or electric motors, but they preserve the environment and they produce second raw material starting from plastic and aluminum caps.
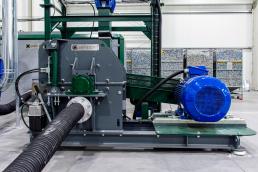
As required by the German government, empty water bottles must not be thrown in the waste; rather they must be recovered from the factories of origin and, once washed and sterilized, they are refilled. The system has been successfully adopted in Germany for many years. The only drawback however is the cap, which must be replaced to maintain a high quality of bottling.
This waste is currently being collected and processed by PIP Processing In Plastics. Founded in Rheinböllen in 2009, the company is structured to work in an End-of-Waste cycle and it produces high quality second raw materials to protect the environment as well. Let’s discover the peculiarities of this company together with General Manager Richard Groß, who recently chose the Panizzolo refining plant for the treatment of its aluminum caps.
Can you tell us about PIP and its peculiarities?
In PIP Processing In Plastics we process caps from German bottling companies, producing high quality second raw material output. Thanks to our strategic position close to these companies, we safeguard the environment by limiting traffic and completing the treatment within our factory.
A whole cap that travels on the road produces much more pollution than the same in granulated version. To our customers we sell aluminum granules and plastic granules divided into polypropylene and polyethylene.
I see that you have hung many environmental quality certificates
They certify how annually we are committed to protecting the environment. Our privileged position allows us to reduce CO2 for the transport of waste. We also aim to optimize transport every year, in order to save more and more carbon dioxide in the environment.
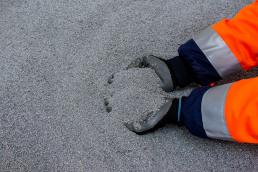
Tell us better about the waste you recover
Until twenty years ago, waste from bottle caps ended up in landfills or incinerators. However, over the years we have become aware of the potential to reintroduce them in the economic cycle. Founding the activity I focused on the quality of the outputs, so as to differentiate myself from the other German competitors.
We have a plant dedicated to the treatment of plastic caps. They are separated from the metal ones, then shredded and then washed. Once all foreign contamination has been eliminated, they are divided into our two qualities: polypropylene and polyethylene.
The plastic treatment line is divided into separate lanes. This is because many times we also buy caps from production waste, which need a different treatment.
Can you explain better what you mean by the quality of the outputs?
The main part of our business is to choose the product to be treated, knowing what we want to achieve in output. Buying new grain is not cheap at all, but with our products we are able to offer a raw material about 25-30% cheaper, maintaining a quality almost comparable to the new one. In this way we can offer our customers a double benefit: savings in purchasing and knowing that they are using a raw material from recycling plants. Important thing in the market, as -German companies are increasingly sensitive to this issue.
Generally we sell to big companies that mix the mixture and blend it to create new products. A part of our customers, who purchase plastic and aluminum granules, works in the automotive sector. Depending on the case, they can be used to produce mudguards, sides, engine covers and more.
Are you the most convenient on the market?
Absolutely not. Around it is possible to recover granules cheaper than ours, but they do not have the same quality. They have large percentages of impurities that can damage the production of our customers at the time of mixing and melting. The reason is given that the input from their plants comes from different scraps, while we are very selective in purchasing.
Our customers keep coming back because they know they find high purity percentage of polyethylene and polypropylene. In fact, the companies that offer lower quality tend to export abroad, while our products are intended for consumption by the German industry, which always requires higher quality
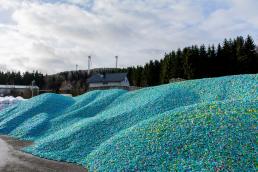
Aluminum caps instead of what procedure follow?
Until recently, aluminum caps were only separated and then destined for treatment in other companies very distant from Rheinböllen.
We obviously realized very early that this way of working was counterproductive both for our business and for our vision of environmental conservation.
Furthermore, we have also seen that the market has been changing in recent years. Some time ago aluminium caps were replaced with plastic ones. However, an increasing environmental sensitivity is changing direction, preferring the use of metal ones. In 2019, for example, the amount of aluminum caps in Germany has grown by 8% and will increase more and more in the coming years.
For this reason, we have decided to internally manage the entire treatment cycle and be consistent with both of our business purposes: Maximize enhancement and help the environment.
An aluminum cap is more expensive to manufacture than a plastic one, however the end customer is increasingly sensitive and prefers to buy environmentally friendly products. The manufacturing companies adapt to this trend and therefore in the near future we will see more and more metal caps.
So the decision fell into a refining plant.
It was the best choice. We went on the market and looked for a supplier that had an excellent reputation and solid experience in waste recycling, especially in the refining of aluminum.
Panizzolo Recycling Systems was suggested to me by asking colleagues and friends from the sector. I was introduced to Mauro Panizzolo, who accompanied me to see his treatment plant near Padua, in Italy.
Having contacts in the peninsula, I asked around and received very positive feedback.
After a test with our material, we convinced ourselves that Panizzolo was the most suitable partner for our needs.
Seeing what the refining plant was operating what was the idea? What about Panizzolo and the outgoing granule?
I am completely satisfied with the system and with how we have been followed in all phases, from the layout to the training of my men.
To be honest there are two aspects that have positively affected me: the fact that it produces little noise and that it does not scatter dust around. All pluses that allow us to work safely with the environment and with staff without having to add other investments.
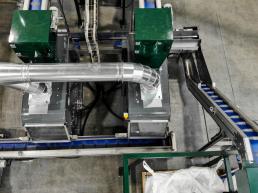
Another thing that pleasantly surprised me is the ability to customize the parameters of the management and control software. A remarkable flexibility and speed of adaptation which is perfect for our types of input waste.
Their technicians are professionally highly trained and they have given to me and to my men all the information to do their best.
Obviously now the most important part is to create our experience, in order to optimize all the functions and set-ups. However, I don’t think there will be any major problems. It is our first time with such a system, but seeing it at work, I am sure there are excellent business prospects.
Have you also seen other recycling plants?
Yes, we had seen another. It was a German company, but in the end it did not have much experience in refining. We also did some treatment tests, but the output quality did not live up to what we wanted.
In Germany how many companies are working this kind of waste?
We are not many in this field. Across Germany there should be a maximum of four or five. There are large companies that treat caps, but only because they collect many types of plastic and metal waste. They are not specialized like us, who produce high quality output. This really makes a difference.
What makes you unique in the market?
What, in my opinion, makes us unique in the German market is the fact of making the most of the metals and plastics coming out of our plants. My customers are interested in using recycled raw materials however they want to maintain a high quality of mixing and melting. Both for the plastic and for the aluminum we help them to assist business and environmental protection.