Let’s start a new cycle of interviews by Panizzolo: Andrea Pensotti Com.Steel
Let’s start a new cycle of interviews by Panizzolo.The first interviewed is Andrea Pensotti, owner and business partner of Com.Steel Spa.
The company is leader in metal and ferrous scrap sector with commercial relationships all over the world. Com.Steel Spa proposes itself as a partner of companies that operate with reliability, professionalism and with respect for the environment. It currently processes and trades all the main categories of metal and ferrous waste.

How was Com.Steel born and how are you working today? Could you tell us about yourself and the company?
Com.Steel was born about 30 years ago from my dad, my brother Edoardo and me. Edoardo manages the whole commercial and production phase while I follow the environmentall and administrative part. For the first 10-15 years we focused on the treatment of electrical cables, with a production of 50-60 ton/day.
Over the years we have decided to diversify the treated material, thus going to touch all various sectors. For the first 14 years, the headquarters were located in the province of Lecco, on a site of about 5 thousand square meters. When we began to diversify and develop the various treatment sectors, the need for more space to manage flows and logistics arose. We, therefore, moved in 2003 to the current headquarters, in Calusco D’Adda, in a space of 20 thousand square meters. In this way, we have managed to further develop the various types of metal scrap, specializing in the world of stainless steel. In recent years we started working with the largest Italian and European steel mills.
Today and future goal of Com.Steel is to treat as many categories of scrap metal as possible and to maximize the enhancement of the contained metals. This allows to be not dominated by the market and to divide the business risk. These peculiarities allowed us to establish ourselves as the main player in the Italian and world market in the purchase and sale of scrap metal; also for this, for three years, we have been working on the construction of the new headquarters.
Could you tell me about your company staff? How many are you and how are the roles divided?
We currently have a staff of around 30-40 people, including an office dedicated to the purchase of metals. At the entrance of the plant our staff checks the compliance and the quality of the material. Then this material is channeled by logistics personnel to the correct loading or unloading area. 11 means allow the handling of the metal scrap, while an internal team of maintenance workers ensures the constant efficiency of the recycling plants. In the new headquarters we will add two electrical machinery for waste treatment, while the forecast for staff is to implement it at least one hundred people. Today 5 people are dedicated to the Panizzolo recycling plant, but they will increase.
How is your presence distributed between Italy and abroad?
Italy always remains one of the most important outlet markets for sale of finished product, economically equal to 80% of the turnover. Unlike the purchase of scrap metal, it is divided in half between Italy and abroad. The sale is only to steel mills and wire drawing mills. Today, Italian steel mills and wire drawing mills are the best sales area in Europe and they are increasingly demanding on the quality of the product they purchase. They are demanding both in terms of product yield-melting ratio and energy consumption. They avoid an unrefined product in an optimal way because it creates additional management and mixing costs in the ovens, in addition to the fact that it does not fall within the internal analysis parameters.
It is necessary to supply the steel mills with a product qualitatively good to buy. If not, natural selection starts: either you are within their parameters or you are off the list of companies from which they buy.
For this reason, in Com.Steel the quality of the product is a determining factor to focus on.
Is this also the vision for the near future of the scrap market?
Absolutely. In the new site that we are building, we have budgeted more than € 4 million to structure a recycling plant complete with grinding, refining and selection of scrap metal. The operating heart is the Panizzolo recycling plant, that is essential for grinding and reducing the material to a perfect size for downstream selection equipment.
Let’s move on to the relationship: Com.Steel – Panizzolo and Com.Steel – Panizzolo machinery.
We have known Panizzolo for a long time and we have been your customers since before you started selling recycling plants, when there was only your car engine grinding activity in the historic headquarters of Piove di Sacco. From here we loaded an average of 2/3 truckloads of crushed iron a day. When Panizzolo started to design and sell recycling solutions, the models of transportable hammermills were so appreciated by Com.Steel that we decided to install one and start treating the tinplate cans from MSW.
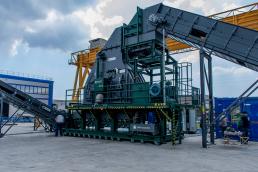
Why did you choose Panizzolo as your recycling plant supplier at the time?
Because my brother and I went to see the crushing plant in Piove di Sacco, the one with which Panizzolo worked daily. We liked it immediately because it was built with the experience of those who work on recycling plants every day. There is a lot of difference between saying and doing.
So direct experience has fundamentally affected the purchase decision?
Absolutely. Panizzolo hammermills have certain details that only the eye of those who work there every day can grasp. Certain precautions that arise only with direct experience. For example: the rotor, the grinding chamber and above all the cradle inserted in the mills. All pluses that Panizzolo has always been able to overturn on the systems it designs and sells.
In your opinion, is this patented interchangeable cradle important in the working of the hammermill?
The cradle is essential for a quick change of the grids during maintenance. These precautions arise only with direct experience: the interchangeable cradle is fundamental; but the fact that Panizzolo has designed a machine that is simple to maintain, with quick access to the grinding chamber is also decisive. We have an internal team dedicated only to maintenance. We keep double cradle and double rotor in order to stop the line as little time as possible. In the long run, avoiding these downtimes also pays for having spare parts in addition.
Did this speed of maintenance and replacement of the cradle and rotor bring benefits over time?
Yes, both during maintenance and for setting changes in the hammermill. With a machine that works about 10-11 hours a day, reduce maintenance downtime has an important impact on productivity.
However, there are other companies in the sector that supply mills with interchangeable rotors.
Yes, but they don’t have the cradle and the change of the rotor and other components is structured in a completely different way. Much more cumbersome.
Working with the first hammermill, has the quality you expected been confirmed?
Absolutely. Besides, for us it is already the third hammermill model that we buy from Panizzolo. We started with a Flex 1000 Mobile in 2014. Then we moved on to a Flex 1300 Mobile in 2016, adding various separation accessories. In the new headquarters, in May-June 2020, we will move on to the Mega 1500 hammermill.
What made you reconfirm Panizzolo also for the Mega 1500 model?
Clearly the choice was due to the construction line. It was maintained at the same quality and professionalism as the previous lines. The mill is bigger but the concept of how it works is the same, if not better. For example the loading system with oscillating table. We have appreciated the previous models, so we have nothing to fear on the next model.
At the beginning you had chosen a mobile system, why this preference?
The reasons were basically two. The first was that they were recycling plants with less required power than Mega 1500. The second problem was space. While in the new site we will have an area dedicated to the new grinding plant, in the current location we had too little space for a stationary plant. The choice therefore fell on the mobile models, compact and complete with soundproofing, loading, transport and first separation.
What is your production?
Today tinplate cans is the second product we load in Com.Steel. With the current Flex 1300 Mobile model we load from 60 to 100 tons/day. Regarding the finished product it depends on how much polluted input meterial is. We produce an average of 80 tons/day.
After the start of the new Mega mill, what are the production plans?
The new Mega 1500 will be used as a roughing machine, preparing the material for the Flex 1300 Mobile. Our experience in material processing taught us many things, the most important of which is that a quality product in output needs the right processing steps. There are no machines that could do everything in one step, whether they are bulky scrap or electric cables. It doesn’t exist because in the end you lose both productivity and quality. In the new location we will certainly increase the flow of incoming cans. From the approximately 2,000 tons / month that we do on average today, we will reach quietly to 4-5 thousand. The whole game will be in how Com.Steel will want to interface with the grids and a fundamental help will come from the interchangeable cradle of Panizzolo of both Mega 1500 and Flex 1300 Mobile. We have no doubt that we could count on productivity of at least 350 tons / day.
Could you give me more information about the new location?
Over the years, the current location has become too small for material flows. Every day 120 lorries circulate between inputs and outputs and about 270 thousand tons of treated metal per day. For this reason, about 3 years ago we started a relocation project to a larger plant.
In the new 66,000 m2 site, the heart of the treatment cycle will be the Panizzolo grinding plant.
With the new site, in addition to increasing productivity, we could expand the range of material treated by Com.Steel. An example is the enhancement of waste produced by other treatment plants. It is still rich in metals and currently it has the landfill as only outlet. With this in mind, we do not rule out the possibility of installing another system, with a Panizzolo hammermill.
What do you think of the slogan “it’s time to maximize the value of metals”, introduced by Panizzolo at Ecomondo 2019?
Certainly, it is more than a slogan, it is an obligation. It is a mission that all companies in the sector should pursue. To continue to have outlet points where selling the product, companies must absolutely follow this path as soon as possible. Foundries, steel mills and wire drawing mills will always want more quality, while the demand in Europe and in the world for waste to be processed has increased, due to the closure of China. Many hope that China will soon reopen its doors, but they will only do it for the semi-finished products for their foundries. The same question for those who, today, are looking for cross roads in other eastern countries. These outlets are valid for the time they are worth, they are unstable and physiologically destined to close.
At the new location will you undertake any environmental policy?
Definitely. Indeed, we are actively acting in this direction. First of all, to take away as much traffic as possible, we built a new road directly, more than 1 km long, and a bridge over the railway. Having an important flow of material treated annually, about 330 road trains will circulate per day and we do not want this to affect the life of the nearby city of Calusco d’Adda. The same trucks will have special parking areas open day and night inside our factory, further reducing the impact on traffic.
Secondly, we are installing a photovoltaic system designed to produce about 2 MegaWatts of energy, intended for the partial use of the treatment plants. Obviously, the remaining necessary power will be supplied by Enel which, as we know, is the first Italian producer of energy from renewable sources.
From your point of view of expert entrepreneurs in the sector, what advice would you give to companies to face the future?
In the world of post-2000 metal scrap there is no room for commerce as we have known it. The present moves towards the processing and refining of metals. The steel mills will saturate the market with the direct purchase of the oven ready product, without the need for merchants. Working the material does not mean installing a shears or a press, but rather producing a finished proler and going as far as possible to recover the waste that comes out of the processing to avoid the landfilling.
Less landfill and more recovery?
As little as possible must go to landfill. In the last two years, also because of the China speech, the cost of transfer has increased fivefold. Landfills are closing and will be completely replaced by waste-to-energy plants in the coming years. For example, all the waste that Com.Steel produces from Panizzolo recycling plants must be completely transferred to waste-to-energy plants. The latter produce energy and heat, so let’s feed a virtuous cycle.
What are the sources of information you draw from for the market?
Being informed about the latest news, today as never before, it is essential for a company in our sector. We are both members and sponsors of SiderWeb, the main web platform for metal market news. We have continuous relationships with companies that monitor and publish statistics. However, it is still essential to speak directly with the major players such as the steel mills.
As a direct user, what advice would you give to a company that is considering purchasing a grinding plant such as a hammermill?
There are multiple points of view to analyze. First of all, the simplicity of maintenance and replacement of components subject to wear, through quick access to the grinding chamber. Then the resistance of the components, the case, the rotor and all the components involved in the processing. We work in an environment where the hammermill is subject to important stresses and is continuously subjected to impacts. The integrity of these parts becomes fundamental in the long run. Obviously the mill is not made only by the grinding chamber. Everything that surrounds the machine is important: efficient feeding, the transmission between the motor and the rotor where there must be quality study and technology. In the end, simplicity must come first: with simple and rapid maintenance, the machine can remain in production for as long as possible.
The essential advice is not to fall into the presumption of wanting to do everything with a single recycling plant.
We must not listen to those companies that offer these solutions. Each product requires adequate hammers, grids and calibrations. When purchasing the first hammermill, we did not have much experience yet, however Panizzolo was able to advise us transparently about which was the best treatment cycle. A trust that we have given him for his direct experience and which is still abundantly confirmed today. In all these years the mills have worked without problems a very difficult material such as tinplate cans.